Prevención De La Corrosión En Instalaciones Petroleras.
Los daños por corrosión en sistemas de fluidos y estructurales es la principal causa de pérdidas económicas son un riesgo de seguridad en instalaciones costa afuera y terrestres sus efectos son previsibles si se toman las consideraciones necesarias que resultan en beneficios económicos y operativos.
La corrosión se forma cuando un átomo metálico es oxidado por un fluido, provocando la pérdida de material en la superficie del metal. La pérdida de material resultante reduce el espesor de pared de los componentes de acero al carbono y aceros de baja aleación, que afectados por la corrosión general se hacen más propensos al fallo mecánico
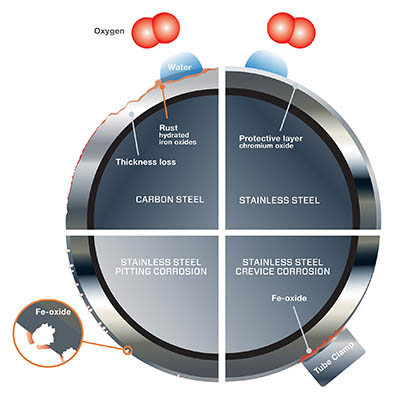
Los sistemas de conducción de fluidos para aplicaciones en instrumentación analítica y de proceso, líneas hidráulicas, aplicaciones en control y servicios auxiliares son típicamente metálicos. En aplicaciones de petróleo y gas el metal está diseñado con un contenido de más del 10% de Cromo, como en el acero inoxidable, el cromo forma una capa de óxido que protege a los metales en su interior de la corrosión. Sin embargo, bajo las condiciones ambientales marinas en las que operan (humedad, temperatura, contaminación), ocasionan que la superficie se degrade y ocurra la corrosión del acero inoxidable.
Diversos factores provocan la corrosión en casi todos los metales. Por ejemplo, el óxido es un subproducto común de la corrosión del acero al carbón, resultante de la corrosión del Fierro y la formación de óxido de Fierro, sin embargo, existen muchos otros tipos de corrosión. Cada tipo de corrosión representa una amenaza que debe ser evaluada al seleccionar el material y su composición, es decir una aleación adecuada para su aplicación.
Piense en una aplicación de proceso que incluye 50 mangueras idénticas. La mitad de ellas se limpian con vapor y se desgastan en un año. La otra mitad no se limpian pero duran alrededor de cinco veces más. Planificar un ciclo de mantenimiento de cinco años para todas es peligroso y podría parar procesos caros por mangueras que fallasen inesperadamente. Pero un plan de mantenimiento anual para todas las mangueras significaría sustituir mangueras con años de vida por delante. ¿Cuánto podría ahorrar la planta si ampliase el intervalo de sustitución del segundo grupo de mangueras a cinco años? A un coste aproximado de 3740 pesos mexicanos por manguera, el ahorro aproximado sería de 357,000 pesos mexicanos solo en coste de producto, a lo que hay que sumar la reducción de los costes de mantenimiento y paradas.
La corrosión en líneas de tubo se clasifica en:
Corrosión por picadura
La corrosión por picadura ocurre cuando la capa protectora de óxido en la superficie del acero inoxidable se degrada, permitiendo que el metal se vuelva susceptible a la pérdida de electrones. Esta reacción electroquímica inicia la formación de pequeñas cavidades.
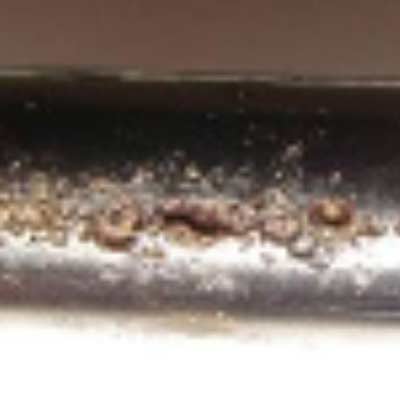
Aunque generalmente se pueden detectar mediante una inspección visual exhaustiva, estas cavidades pueden crecer lo suficientemente profundo como para perforar una pared de la tubería por completo. La corrosión por picadura también puede facilitar el inicio de grietas en los componentes sometidos a tensión. El medio ambiente con altas concentraciones de cloruros, incluidos las creadas por la evaporación de las gotas de agua salada depositadas en la superficie del metal, favorece a la corrosión por picadura, especialmente a elevadas temperaturas.
Al examinar tuberías de metal en busca de corrosión por picaduras, habrá que buscar los depósitos de óxido de Fierro de color marrón rojizo, así como posibles cavidades que pueden haberse formado en la superficie del metal.
Corrosión por intersticial (grietas)
De forma similar a la corrosión por picaduras, la corrosión por grietas se inicia con la descomposición de la película protectora de óxido del acero inoxidable y continúa con la formación de orificios poco profundos. Sin embargo, en lugar de ocurrir a simple vista, la corrosión por grietas, como su nombre lo indica, ocurre en las grietas.
En un sistema típico de conducción de fluidos, existen grietas entre los tubos y los soportes o abrazaderas de los tubos, entre los tramos adyacentes de los tubos y debajo de la suciedad y los depósitos que pueden haberse acumulado en las superficies. Las grietas son prácticamente imposibles de evitar, es decir, las grietas por apriete representan uno de los mayores peligros para la integridad del acero inoxidable. Esta corrosión ocurre cuando el agua de mar penetra al interior de una grieta, lo que lleva a un ambiente químicamente agresivo donde los iones que causan corrosión no pueden difundirse fácilmente fuera de la grieta. En tal escenario, toda la superficie dentro de la grieta puede corroerse rápida e imperceptiblemente.
La corrosión de grietas solo se puede observar visualmente cuando, por ejemplo, se retira una abrazadera de la tubería instalada. Es importante recordar que la corrosión por grietas puede ocurrir a temperaturas más bajas que la corrosión por picaduras.
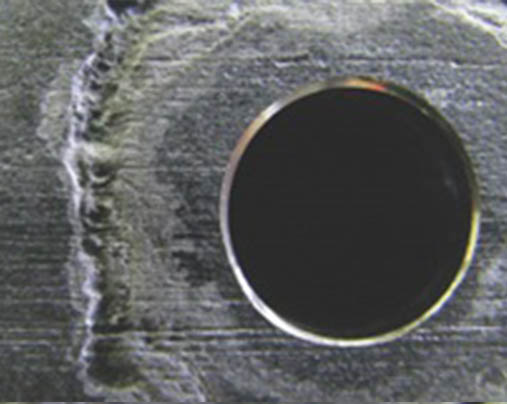
Seleccionar el Material Adecuado para la Resistencia a la Corrosión
Una plataforma petrolífera puede tener más de 15.000 metros de tubo, más de 20.000 componentes para sistemas de fluidos, no menos de 10.000 racores y unas 8.000 conexiones mecánicas. Por eso es importante elegir metales resistentes a la corrosión en el proceso de selección de materiales.
Hay muchos aspectos a tener en cuenta para ayudar a gestionar la corrosión cuando se especifican los materiales:
Inspección de la calidad del material de nuestros proveedores.
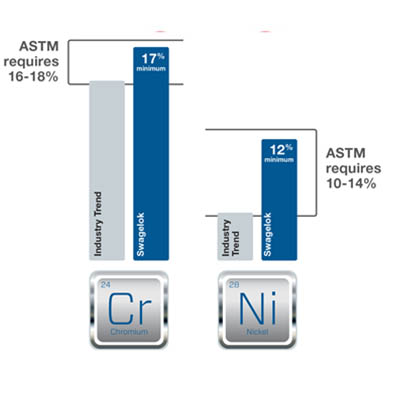
La mejor forma de evitar un problema es detectarlo antes que aparezca. Y una forma de hacerlo es asegurar que el proveedor tiene implementadas medidas de control de calidad estrictas para evitar la corrosión, empezando por los controles del proceso e inspección del material en barra saliente. La inspección puede tener muchas formas, desde la visual para asegurar que el material no tiene defectos superficiales, a los ensayos específicos que detectan la susceptibilidad a la corrosión.
Otra forma en que un proveedor puede ayudarle a verificar la idoneidad del material es comprobar los niveles de elementos específicos en la composición de éste. En relación a la resistencia a la corrosión, resistencia, soldabilidad y ductilidad, el punto de partida es una aleación de una composición optimizada. Por ejemplo, cantidades mayores de níquel (Ni) y cromo (Cr) en el acero inoxidable 316 que las mínimas exigidas por las especificaciones de la normativa de ASTM International® (ASTM), resultan en materiales más resistentes a la corrosión. El proveedor debería siempre ofrecer la composición química de los materiales e indicar el cumplimiento de las normativas publicadas por la International Standards Organization (ISO) y ASTM.
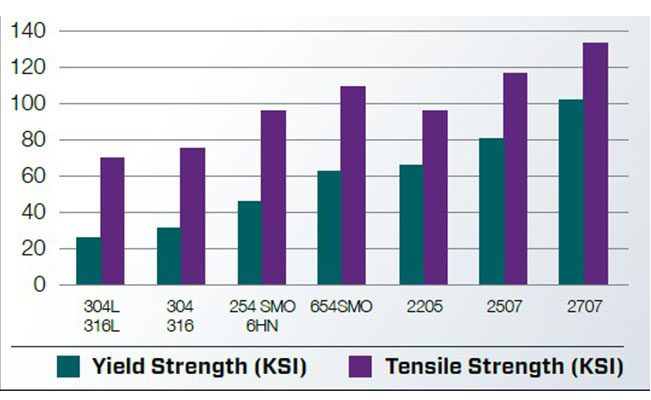
Propiedades Mecánicas
Las propiedades mecánicas de los materiales incluyen su límite elástico y resistencia a la tracción Los materiales más resistentes se pueden utilizar para fabricar componentes que deben trabajar con fiabilidad a altas presiones.
Compatibilidad del Material
La corrosión puede ser un problema caro. La National Association of Corrosion Engineers (NACE) estima unos costos anuales en miles de millones de dólares para toda la industria de producción de petróleo y gas. Pero el poder identificar visualmente y saber dónde buscar la corrosión puede minimizar el riesgo. Mejor aún, si los ingenieros pueden prever la corrosión y elegir bien los materiales, mejoran la integridad del sistema, la longevidad de los bienes, el rendimiento y la seguridad.
Siga estos pasos para reducir el impacto de la corrosión en sus aplicaciones:
Asesoramiento Continuo
Instalar componentes para sistemas de fluidos hechos con materiales de primera clase es solo el principio. Para asegurar la longevidad de sus aplicaciones, es vital tener asesoramiento continuo. Asegúrese de seleccionar un proveedor que conozca sus retos y que pueda recomendarle y aportar soluciones que protejan sus inversiones en materiales.
Para ampliar la información sobre nuestras propuestas de formación en la selección de materiales porfavor contactenos.